How to confirm the process parameters of UV curing process?
The curing of various compounds in the UV curing process involves fundamental criteria for light intensity. When the energy intensity of the curing light source does not satisfy the requirements, the quality of the cured product suffers, thus determining the ideal curing energy intensity is the most critical step in the UV curing process. The Linshang UV energy meter is not only capable of detecting UV energy and intensity, but it can also record curing time, making it ideal for assisting engineers in determining curing process parameters.
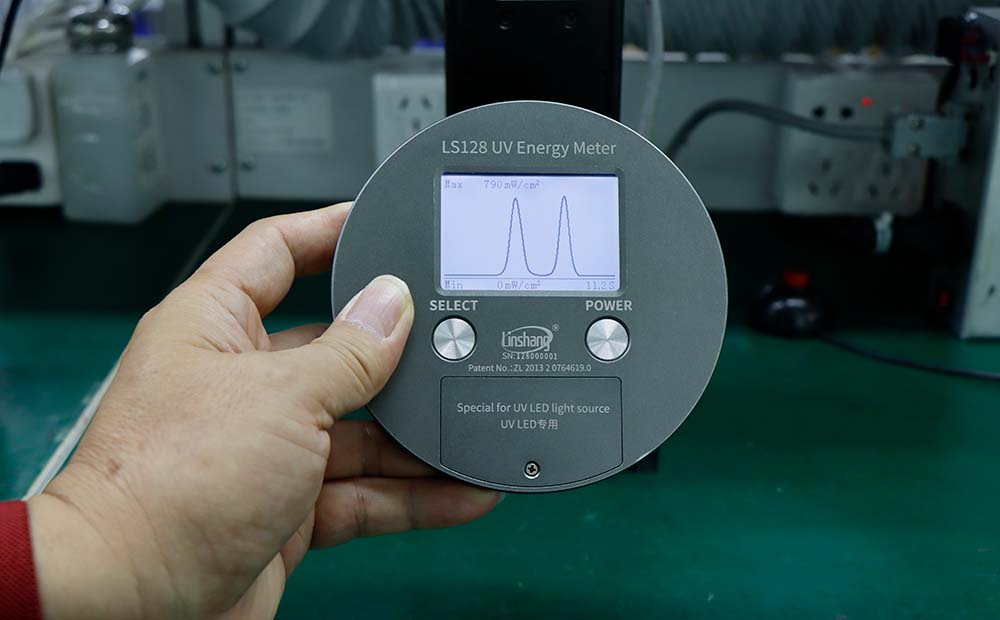
What are the process parameters in the UV curing process?
In the UV curing industry, the following important process parameters need to be identified: light source type, light source power, energy value and curing time.
Generally speaking, the light sources used for UV curing are mostly high-pressure mercury lamps and UVLED lamps. In the UV curing industry, high-pressure mercury lamps use its ultra-high temperature to cure the product, the advantages of this type of light source is low cost, high power, strong lighting effect. The disadvantage is that they are not environmentally friendly. With the development of technology, UVLED light source has gradually replaced high-pressure mercury lamp as a new curing light source. UVLED lamp is more environmentally friendly than high-pressure mercury lamp, energy saving, and the use of no advance preheating, to save time costs. In addition, different curing light sources require different curing energy, curing energy is the product of the average power of the light source and the curing time. Ultimately, these four process parameters of light source, power, energy and curing time affect each other.
Why is it necessary to confirm the curing process parameters?
There are two main reasons for confirming the curing process parameters.
-
To confirm the curing time to ensure the consistency of the processed product
In the same production line, the curing light source consistent, so you want to cure energy intensity consistent, it must be fixed on the curing time and curing power. Usually, the UV light source after a period of time will inevitably appear power attenuation phenomenon, for process engineers, in the discovery of light source attenuation, only by replacing the curing lamp to achieve the purpose of balancing power, but often replace the lamp, it requires a large amount of cost. So when the lamp has not decayed to a certain extent, control curing energy means control curing time, so as to ensure the same long line of processed products of consistent quality.
-
Ensuring efficiency
The fundamental reason for the efficiency of modern companies is the development of standards. A proper standard saves time costs and reduces unnecessary waste. This statement is also appropriate in the UV curing process, to determine the curing process parameters to ensure that the same production line or even different production lines to produce the consistency of the quality of the product, as much as possible, can greatly save human and material resources and improve production efficiency.
How to control the process parameters of curing?
Process engineers confirm the measurement environment, consistent light source, consistent test instruments, consistent measurement distance
Debug a calibration data. Engineers through a number of experiments, and constantly adjust the light source distance, curing time (conveyor speed, etc.), to get the best a total curing energy value, the energy value as a standard value. In the commissioning process, engineers can use the Lin Shang UV energy meter to detect the curing energy and power emitted by the light source, and record the curing time.
Different production lines of the same type of light source to take the best total curing energy value comparison, to get a suitable for this type of light source of the best curing energy value, as the standard value of the total production line.
The same light source, different time test, after the light source decay, by adjusting the curing time to maintain the best curing energy value.
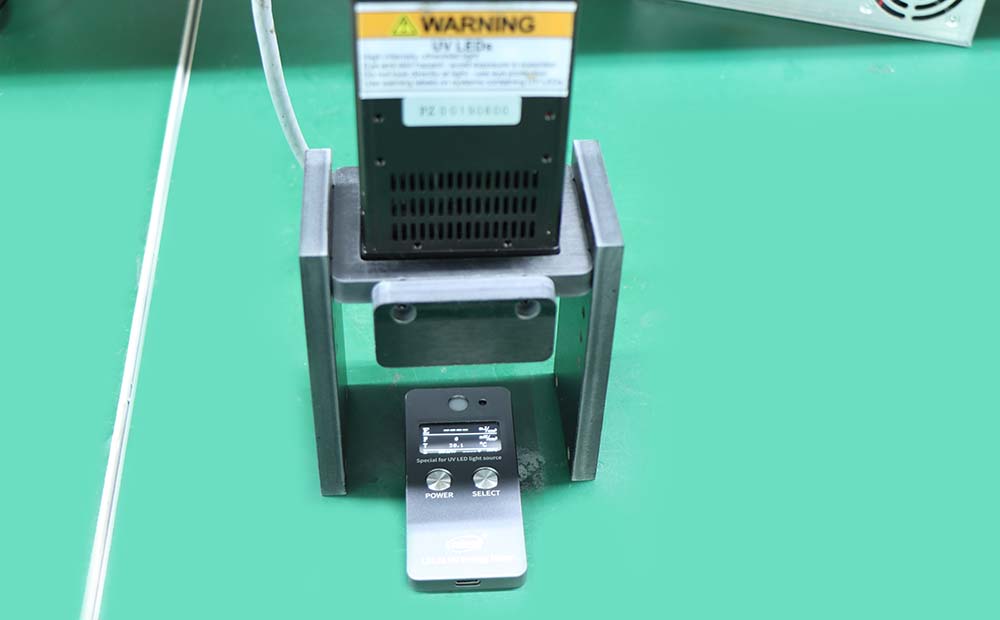
UV curing lamp
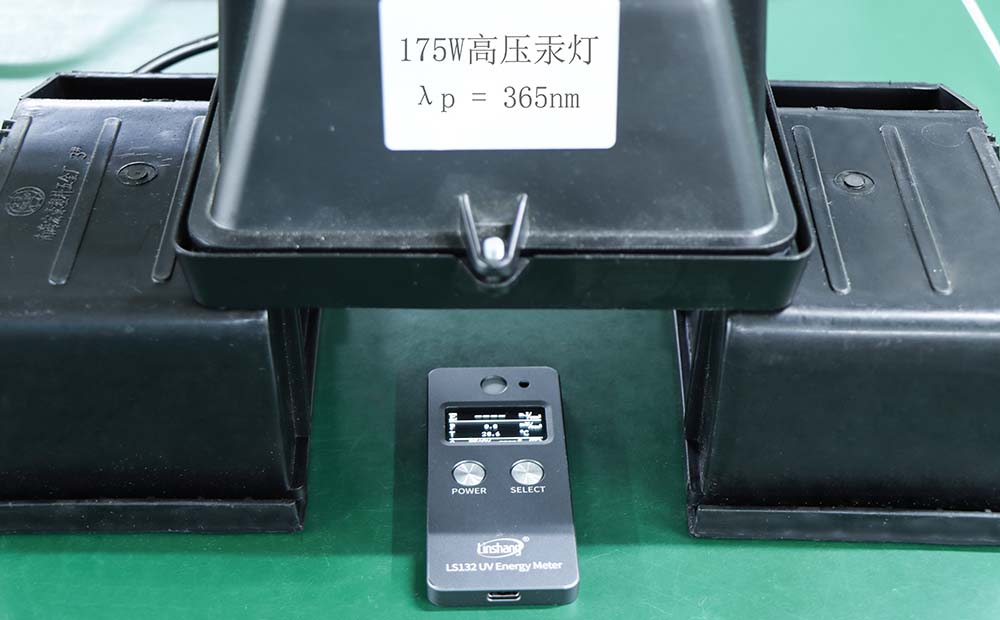
UV energy meter to detect the energy intensity
What are the advantages of ultraviolet curing in the use of the process?
1. The use of ultraviolet curing, can greatly reduce the cost of personnel and time costs, machine automation operation is convenient and fast.
2. UV curing in the use of the process will not occur in the solvent volatilization phenomenon, so that there will be no pressure on air pollution, which is also a major feature of ultraviolet disinfection.
3. The use of ultraviolet curing machine can reduce the cost of product production time, and effectively improve the productivity of the product to bring greater profits.
4. The use of ultraviolet curing machine space requirements are relatively very small, which can also reduce plant costs.
5. The use of ultraviolet curing products made of strong monitoring controllability, you can use UV energy meter to detect the energy intensity of the UV curing light source. To ensure that the finished product qualified rate.
The reason why the ink does not dry in UV curing
1. UV curing lamp energy is not enough, in the curing process, the energy of the UV curing lamp directly determines the qualification rate of the finished product and whether it can complete the important factor of curing. So we use UV curing, as often as possible to use UV energy meter to detect the specific energy intensity of the UV curing light source is how much, only then can ensure that the product qualification rate and UV curing effect.
2. UV curing lamp and ink drying coefficient does not match, we use UV curing lamp, we must choose to match the intensity and wavelength of the drying coefficient. Specific intensity band can also be directly used to detect the UV energy meter to know.
3. Ink printing is not immediately after the completion of the use of UV curing, or stop a long time before the start of UV curing, so that the chemical composition inside the ink is easy to volatilization and deterioration phenomenon, so it will cause the ink can not dry phenomenon.
4. UV light source is not directly irradiated to the surface of the cured product, the product in the curing time, must ensure that the full range of UV light source irradiation, if the product does not receive the energy of UV light, it is easy to lead to poor curing effect.
In summary, the above problems are mainly due to the product in the curing process requires the intensity, energy and time is not well controlled, such as how strong the UV curing lamp, how much energy is needed to make the ink curing fully formed, how long it takes and so on these issues. Because of this, we are in great need of a professional UV energy meter to conduct real-time testing of product curing and data recording, through analysis and comparison, the development of a fixed program to detect UV curing machine can work properly.
- How to Detect the Transmittance of Materials with Transmission Meter?
- UV Power Puck With Probes for Various Industries
- Paint Thickness Gauge with Bluetooth for Secondhand Car
- Inspection Method of Digital Coating Thickness Meter
- How to Measure UV Light Intensity of Germicidal Lamps?
- What optical and digital zoom mean